Over on our Podcast you can now listen to our latest interview with Di and Debbie, from the world famous Appletons brand of crewel and tapestry wool. For nearly 200 years, they have been used across the globe in some of the most prestigious tapestries and embroideries in cathedrals, stately homes and government buildings.
Founded in 1835 by Thomas Appleton, Appleton is just as evangelical about British wool today as he was back then. All 425 colours are dyed and spun in Yorkshire and the wool is 100% British. The range, which is available in crewel wool, which is a two ply yarn, and tapestry, which is a four ply yarn, still incorporates all the William Morris shades.
As well as featuring a contemporary colour palette, the wool is used by modern and traditional designers, stitchers, weavers, needlework schools and rug restorers throughout Europe, Asia, Australasia and North America. More recently, Appletons have also worked with needlepoint designers to launch a range of tapestry and embroidery kits under the Appleton’s brand, all of which are hand assembled in Buckinghamshire today. Appleton’s prides itself on the quality and consistency of the wool they produce and on creating distinctive, beautiful, kits art of stitching.
Listen to the podcast below or have a read through while looking at some of their beautiful products.
Textile Talk with Appletons Wool
Listen to the podcast now or read through the transcript below.
Textile Talk Appletons
Transcription
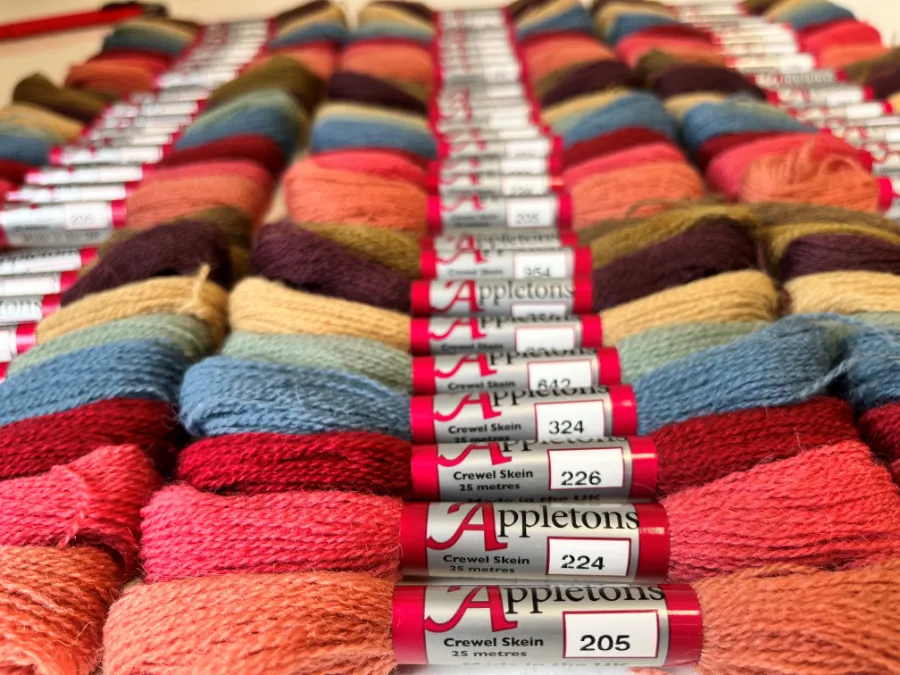
Gail: Thank you so much to both Debbie and Di for joining me this morning on this Textile Talk podcast. It's lovely to speak to you, and I really appreciate you taking the time out of what I know is a busy day to be here today.
Debbie: That’s right. We’re delighted to be here.
Gail: So the first thing that I'd perhaps like to start off with is a little bit of history, if I may. So I realised that Appletons have a long history and they've been producing yarn for quite some time, probably long before any of us were around, definitely. So could you tell me a little bit about how you personally became involved with Appletons?
Di: Well, yes, it does go back a long way, back to the 1850s, when the wall was when it started, because of the arts and crafts movement, who were doing a lot of tapestry in those days. William Morris and William Morris and all his gang. And they produced the colours that William Morris needed, which are still in our range, actually. And then it stayed within the Appletons family right until 2013, when the last Appleton sold it to me.
So we’ve been going now for ten years, and now it is purely and simply a wool company with 425 colours of wool. And then the last three years, we’ve slightly diversified in that we are now making kits, which we’ll get to a little bit later. And we can tell you a little bit more about the wool, too, later on. But that’s a brief resume.
Gail: And what made you want to buy it? I mean, did you have knowledge of it beforehand?
Di: Yes. Oh, I’d always used Appletons all my life. And I’ve always been involved in embroidery and tapestry. In fact, I lived in the States and taught it there and then came back and then the opportunity just presented itself and someone said to me one day, Die, you should buy the business. And I did. Otherwise I think it would have gone to the wall, which would have been very sad. And I was so anxious for it not to die. And the rest is history that we’ve grown and the business is doing so well now. So it’s a very happy story.
Gail: Oh, that's lovely. So what is it that you've changed about the business to bring about that turnaround?
Di: Well, we’ve probably, most importantly, brought it into the 21st century. When we bought it in 2013, they didn’t own a computer, so if you can imagine where that’s gone. And now we’re almost entirely online, and as is the whole of the sort of people who are selling our wool are selling it online around the world. And obviously we’ve moved on in a major way.
Gail: Not computerised before 2013. That sounds almost impossible, doesn't it, in today's age?
Di: When I bought it, they had one typewriter and that was the only thing that they used. And all the machinery was incredibly old. Most of it was 100 years old. So we’ve replaced all our machines. Now we’re buying new machines as we speak, and it’s changed. We also moved it out of London, so we’re now in Oxfordshire, but not that that really makes a difference in today’s world.
Gail: Well, yes, that's true. So has the actual process of making the wool, has that changed at all?
Di: No, that hasn’t. Nor has the source in that all our wool is still sourced from Bradford, which is the centre of the wool world in the UK. And this is all 100% British, which is as it was and always will be. And Debs can go into that with a little bit more detail about where the wool comes from.
Debbie: Yes, basically, we buy all of our wool from the British Wool Board. So I don’t know how much you know about the British Wool Board, but it’s basically a collective owned by about 35,000 sheep farmers. So it’s a UK collective and we buy our wool from there. And we use effectively, I suppose, like a wool trader. And the way that the British Wool Board works is they hold auctions. I think they have it’s something like about 13 or 14 a year. And so he will effectively they’re all online now, though. But, I mean, he will effectively buy wool at one of the auctions. And we’re quite specific about the type of wool that we require.
So, because we dye so many different colours, some of our colours, for example, are very pale colours. So in order for those colours to take the wool that we buy, or our buyer, when he goes to the auctions, he makes sure he gets the whitest wool he possibly can.
The UK wool isn’t as bright, for example, as Australian wool, but we are absolutely determined to make sure that we keep everything British, that we support the British textile industry. So we’re very careful and picky to make sure we get the whitest wool we possibly can from British sheep. But we also have to be quite careful about the length of fibre that we buy. And so if you’re doing a tapestry, for example, you don’t want to have a fluffy tapestry at the end of it, which is quite different if you wanted a nice, soft, fluffy jumper. So the wool that you would select for tapestry wool would be quite different to the wool that you might select if you were looking for a knitting wool.
So we are quite specific about the length of fibre so that we make sure that we don’t have, like, what we would call a beard on the wool. We’re quite specific about the colour of the wool. We look for a uniformity in the crimp, we look for strong fibres, because if you’re pulling it through a canvas, we don’t want those fibres to break. So often people will say to us, well, what breed of sheep does your wool come from? And we can’t really answer that because it might come from five or six different breeds. But what we’re looking for is not the breed necessarily, but the fibre length, the colour. And that can all be determined by environmental factors as well as breed. So that’s what we’re looking for. And we’ve been dealing with the same wool trader now for gosh. I think he has records, I think, going back to the 1960s and 70s. So we’ve been working with the set.
He really knows what we need, which is great. So yeah, so that hasn’t changed at all. But then the wool, then, once it’s been purchased, it then gets scoured and cleaned and effectively turned and combed and turned into what we call a top. And then that top then would go to a spinner. And this is all done in the UK. Our spinner is in the UK. And they will spin our wool to our specifications. And in that case, it’s two different specifications that we have because we sell two different types of wool. We sell tapestry wool, which is a four ply, and we sell crewel wool, which is a two ply, but also within those ply. I’m getting very technical here. Do you want this much?
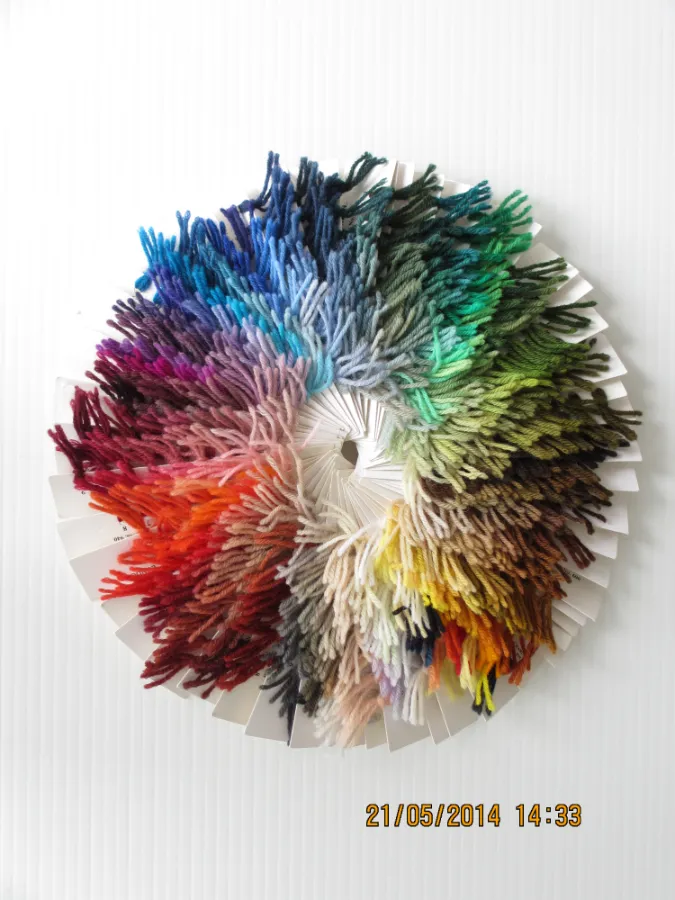
Gail: No, absolutely. Yeah, certainly do.
Debbie: The two ply wool, we call it a, refers to the diameter of each of the strands. So in two ply, you’ve got effectively two strands, and our four ply is four nines, and the nine refers to the thickness of the strand. So our two fourteen s, the crewel wool, has got thinner strands in than the tapestry wool, which has got thicker strands in.
So the higher the number the smaller the diameter. Weirdly. But basically we have it spun completely differently for the two wool, the two thicknesses that we do. And then it’s plied again at the spinners, then it gets sent to our dyers, which is also in the UK. And the dyeing is done. Certainly, I’m sure it wouldn’t have been done necessarily like this when William Morris was using it. It probably would have been far more natural dyes. But because of the way that you dye wool, you have to use an acid dye because an alkaline will destroy the wool. So we use acid levelling dyes for our wool.
And again, because if you’re doing a tapestry, it’s a bit like if you’re buying wallpaper, for example, you need to make sure that you buy from the same lot. And with our wools, we frequently have people who have got through or halfway through a tapestry and they’ve run out of wool, or they’ve found a tapestry that their granny had done 50 years ago and they want to finish it. And so we’re really, again, really picky about making sure that our colours are consistent. So from that perspective, we’re not able to use sort of natural dyes because you wouldn’t be able to get a consistent colour.
And that’s really important for us because we want people to know that if they’ve started a tapestry 50 years ago and they come back and they try and buy the same colour, that no, it’s not going to be from the same dye lot, but it should be pretty jolly close. So we use acid levelling dyes and then once the wool’s dyed, it then comes here. And as Di was saying, our machines have changed quite a lot from when Di bought the company ten years ago. So it’s much more automated. Here we have one guy who looks after all of our machines for us. So what we do here is we turn the hanks of wool. We can put it on cone now, or we turn them into the small skeins that have got the sort of Appletons wrapper around that people will recognize.
Gail: And why would you put it onto a cone? Is there some reason that someone would need that amount?
Debbie: Yeah, often. So if you’re weaving with wool, for example, you would want it on a cone. And that’s something quite recent, that’s something quite new for us. So we’ve always had to put because our wool is dyed in batts, there’s two different ways of dyeing wool. You can dye it by hanks, which is where you effectively, you almost hang all the hanks and then they get sort of dunked into a big VAT of dye.
Or you can do something called package dyeing, and that’s where the wool is put onto a cone, and then the dye is sort of forced through at quite high pressure through the cone. And that can dye it that way. But because, again, because of the nature of what our wool is used for, which is tapestries and embroideries. If you dye in the package dyeing way, which is how most wool is dyed, actually, what can happen is it can really affect the fibres because pressure is being put through at such a high the dye is being put through such a high pressure that that can cause a problem with the fibres. But also, you can get uneven dyeing.
So in order to get the most even dye you can, which is the least harmful to your fibres, we dip dye it effectively. So it’s called hank dyeing. So we’ll dye it on a hank and we’ll then back wind that onto a cone in order to then wind it onto the smaller skeins. But also, as you said, why do people want it on cone? So, previously we hadn’t sold it by cone, but now we’re finding that some of our larger kit companies want it on cone. Because if you’re putting together a kit, you might want, I don’t know, 10 metres of one colour, and you might only want 1 metre of another colour, depending on what your design is.
And if it’s on cone, you’re putting exactly what the customer requires into the kit, as opposed to putting in a hank, maybe when you only need a quarter of a hank or putting in a skein when you only need enough to do two eyes. Does that make sense?
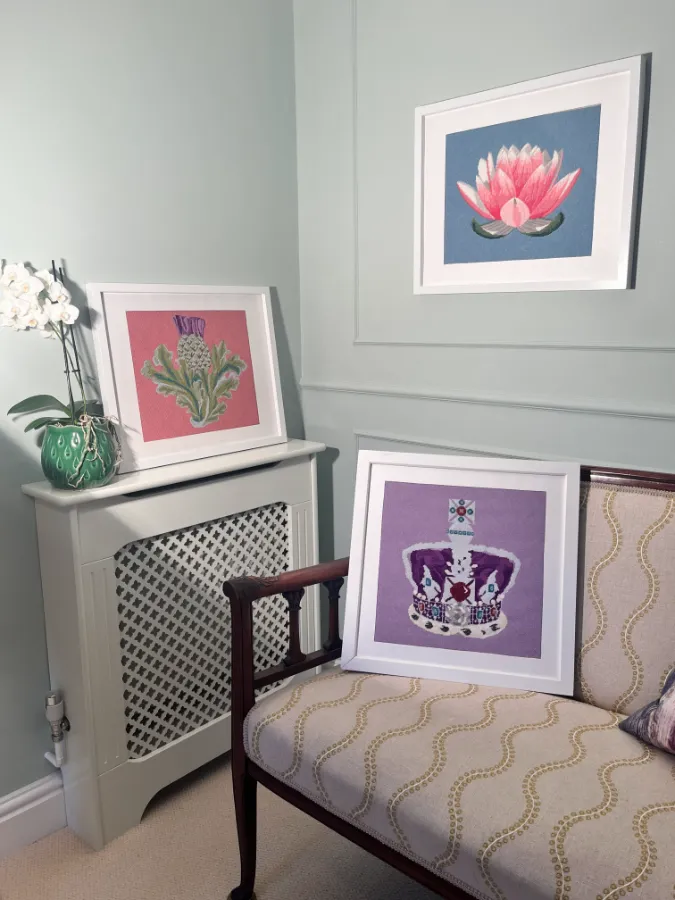
Gail: Yes. No, it does, completely. So in that case, obviously someone would be packaging their own kits. But do you package kits as well?
Debbie: We do. So we have a range of our own kits that we obviously put together, but we do offer some of our customers will put together their kits, so they’ll give us recipes effectively. And then we’ll put those together in a sort of wool bag, and we’ll send it to the customer, and then they’ll put it together with their design.
Often people will order I mean, that is a big part of our business, is kit making. So often people will order the colours they need and they’ll put the kits together themselves. It just depends on whether they want to use that. It’s very time consuming putting wool bags together. So I guess it depends how they.

Gail: Are, how they're yes, I can well imagine. If you sort of had to compare your yarns with, obviously something like DNC or whatever, what would you say the main differences are?
Debbie: Of we have very few competitors that do crewel wool, and the competitors that do do crewel wool, they wouldn’t do the range that we do because we do all 425 colours in both weights. So with crewel wool, there isn’t really I mean, there’s a few others, aren’t there Di, but there’s not really very many.
Di: Particularly in America.
Debbie: Yeah, in America, there’s more people doing crewel but yeah, there’s not very many competitors who do crewel wool with tapestry obviously, there are more competitors. You’ve got DMC. You’ve got anchor. But I would say our wool is the best thing about our wool is the fact it’s British, and I think that stands for a lot, to have low wool miles. It’s all done in the UK.
You’re supporting British industries? We’re supporting British farmers, the British textile industry, British Dyers, British spinners. And I think if you go back wool was the UK’s biggest export. If you go back 500 years, which in fact I did about a month ago, you go up to Bradford and you go to all of those mill towns and you see the big old mills and how so many of them have been turned into flats and things.
It’s just so amazing to walk into a working mill that has been there. I think the one that we use was definitely was it pre Victorian? No, it was Victorian. So it’s been around for over 100 years, and to walk in and to think about the history and how you feel like you’re supporting that industry and it’s so important to the UK. I think that’s the best thing about our wool is that wool starts off by being incredibly environmentally sound. It’s unbelievably sustainable. A sheep will grow a fleece every year. So from that perspective, it’s great. But then also just the fact that with us, it’s very low wool miles, it’s the furthest it travels is from Bradford down here. That’s what I would say.
Gail: And we do hear a lot, don't we, about supporting our farmers, particularly sheep farmers at the moment, because they struggle. I think the price of wool has generally gone down for them, at least what they receive has.
Debbie: Yeah. And when you see, as I said, as I did again a month ago, and you go through these mills and you go through the processes that the wool then goes through, you think, Crikey, I can see why I’m surprised it’s not more expensive. When you see the amount of machines it has to go through to get to the state that it is when it lands in a customer’s hands. Yeah, it’s quite phenomenal. And you’re right, it’s absolutely vital to support the British farmers.
And we’ve just gone through quite a big exercise with the British Wool Board, actually, in making sure that our wool is completely traceable. So we went back and we had to provide lots of information about who we used to spin our wool, who we used to dye to create the tops where it’s bought. And they were then able to enabled them then to get it back to a certain auction and to actually make sure the whole process of where it’s being bought from, that we know exactly where it’s coming from, you can trace it back to the lot it’s being bought from. And therefore then the farmers. And that’s really important to us.
Gail: Yes, you did mention natural dyes previously and saying, obviously, that they are not consistent enough for you to use. But do you perhaps consider other processes whereby the ecological impact of dye is lessened?
Debbie: Yes, so two things on that front. Firstly, we now sell undyed wool. So if people do want to dye it themselves, which actually is increasingly, you do get lots of people who want to just small sort of cottage industries, they want to do their own dyeing using their own natural dyes that they might have sourced. So we now do sell undyed wool for people to do that with. But yes, you’re right.
And when I’m talking about the environmental impact on wool and the sustainability, probably the least sustainable bit is the dyeing. By the very nature of the fact that it requires quite a lot of water, it requires you to heat that water up to a certain temperature. But what our dyer does is they’re part of, I suppose for want of a better word, an environmental club called the IPPC. And what they do is they have to make sure that they have signed up to certain procedures and regulations, specifically with the Yorkshire water, that the effluent that they create, it doesn’t get discharged until it’s at the right PH, it’s at the right temperature, they have to make sure there’s no sulphide, no chemical oxygen in it.
So there’s an awful lot of rules and regulations that our dyers have to adhere to in order to actually dye the wool. So, yes, it needs chemicals, but they try to be as environmentally sound as they can. They recycle their water as much as possible because it’s in their interest to to keep that hot water as much as they can, because, you know, they want to burn less gas, which is how the water is heated up. But you can’t get away from the fact that if you want consistent colours and you want a consistent range. And the way we sell our wool is we sell it in a range. So we might have a colour, for example, sort of grey green or something, whereby the colours go from very light to a very sort of dark colour.
So within one range you can get maybe nine different colours so that you can do sort of quite nice gradation on your tapestries. Now, you couldn’t achieve that if you were trying to do it really with natural dyes, I don’t think, not to keep to be consistent. So it’s a balance between making sure that you’ve got a really consistent dye, but that is also as environmentally sound as we can possibly make it. And I’m really confident that having also just been up to see the dyers that that is happening.
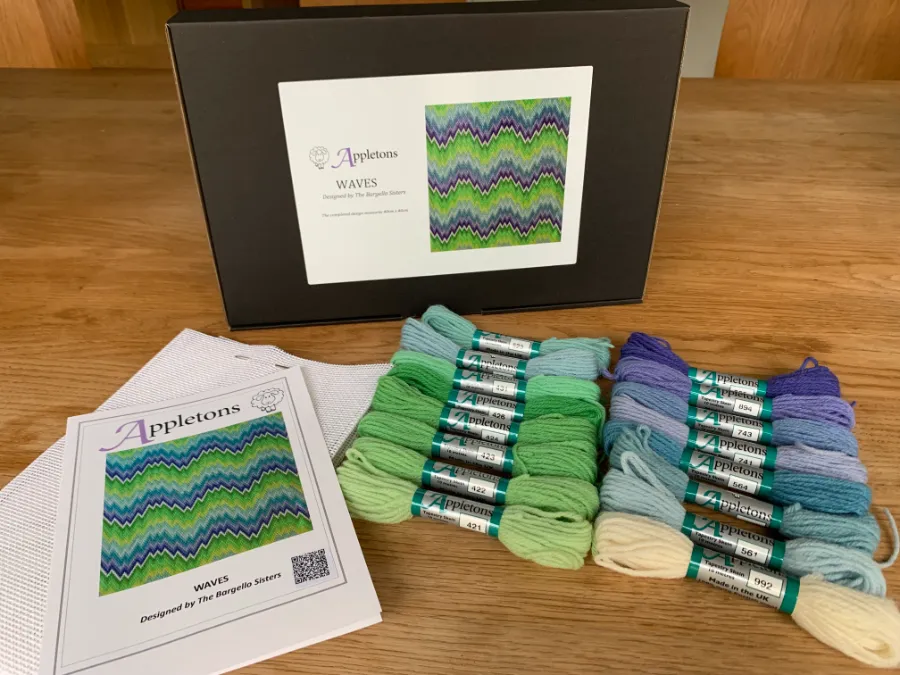
Gail: There is always a compromise to be had, isn't there, with these things? And ultimately, if you want colours that you can rely on purchasing time and time again, if you run out part way, then you do need something that is reliably dyed and obviously you perhaps might be washed, you don't want it to run. So there are things that you do require in a thread.
Debbie: And that’s quite an interesting point that you just made, because when you’re dyeing a product, what we look for is, yes, we do obviously make sure that it’s as colour fast as it can be. But what’s more important to us is that it’s light fast. Because again, if you were dyeing something for clothing, what’s number one in your mind is that this has to make sure that this is going to be washed.
We need to make sure it can go in the washing machine or it can be hand washed to a certain temperature. Now, if you’re dyeing wool that’s going to be hung on a wall or it’s going to be put into a cushion, it’s going to be left in a room, it might be on a sofa, it might be in front of a window. What’s really important to us is that our colours are as light fast as possible. And so often there’s a balance again there. So we tread a very careful balance in making sure that number one in our mind is how light fast is this colour. And the stronger the colours, particularly with oranges, it can be a real challenge to get them to be light fast. It’s much easier to have a light fast, obviously, cream or paler colour, but actually, some of the really strong colours, we have to make sure that our colours are light fast.
If you’re using that wool to stitch something that is ultimately going to go on the wall or going to be turned into a cushion for a sofa, foremost in your mind is, is this going to fade in the daylight? And so we need to make sure that we use dyes and acid levelling dyes are reasonably good at this, but we need to make sure that we use dyes that don’t fade in the daylight. So our dyes are constantly tweaking colours. And in fact, we brought out a new range recently and it was really tough to do because the range we brought out was a sort of neon range. And the brighter the colours, the more difficult it is to get them light fast. So it’s a constant balance making sure that the recipe that you use is as light fast as possible. That’s not to say that we don’t consider it being colour fast in water. We do, obviously, because we understand that people might need to sponge clean their tapestries. So we do pay attention to that, but we pay more attention to it being light fast.
Gail: And would you recommend that somebody did wash if they perhaps embroidered a cushion using crewel wool that they'd be able to wash it at the end. Is there anything specific they would have to do to care for it?
Debbie: So what we say is that we just recommend that you sponge clean the wool, that you don’t put it through the washing machine. That’s not to say some of our colours you can put in the washing machine. It depends on whether or not it’s sort of a very bright, bright colour. So some of them we’ve gone through some trialling processes, and we have put them through, and they’ve been absolutely fine. But because, as I said, we focus far more on it being light fast, and you can’t have both, necessarily. So that’s why we recommend just sponge clean it really right.
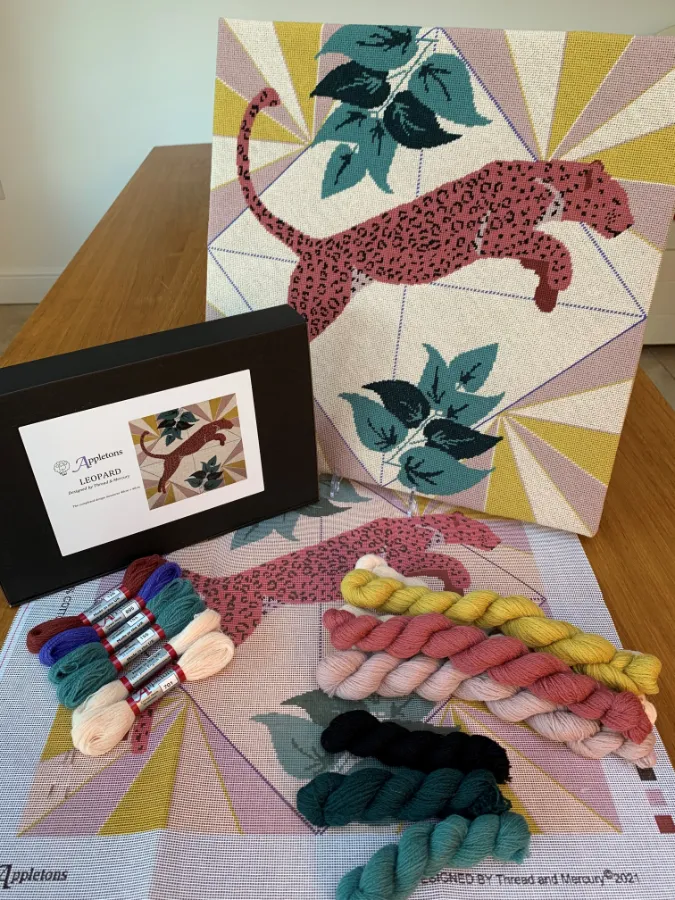
Gail: And if you did subject them to water, would they run, or would they stay as they are?
Debbie: No, I mean, it depends on it’s a bit of a sliding scale, so it depends on the temperature of the water that you’re subjecting it to. In fact, Di might talk a bit more about this. We do recommend that once you for example, once you’ve actually stitched your piece, you can then spray it with water in order to stretch dye. Maybe Di can speak a bit of that.
Di: Yes, I do. Everything I do, I will spray it. I using a soft water spray and then obviously stretch it. I’m sure anybody who does any sort of embroidery or tapestry knows that that’s what you do at the end of the end of it and to square it off more than anything else. So it can certainly take that without a problem. Certainly wouldn’t put it into hot water or into any sort of detergent or any sort of washing machine or that’s out of the question.
Gail: Okay, that's fair enough. So, actually, following on from that, do you have any tips for using your yarns within embroidery or if someone's doing tapestry?
Di: Well, the range of people using our wools is huge, and it’s quite interesting because it’s very different all over the world. For example, the Far East, China, Japan, South Korea, where we sell quite a lot of wool, only use crewel wool. They don’t ever, ever use tapestry wool in America. It’s a mixture. But our wool can be used on canvas, as I’m sure you can imagine, for all sorts of purposes. And it can be used to make carpets. It can be used to make wall hangings. But it can also be used particularly the crewel wool can be used on linens and soft fabrics and for other purposes. So it’s also used by rug restorers around the world who are repairing very old antique rugs. It’s now used for making new rugs, so the uses go on and on.
Gail: I know when I have used because I've used both the Kroll and the tapestry wool of yours, and the main difference that I notice using it in a tapestry sense on canvas on canvas. Yes. The main thing that I've noticed is that it isn't woven quite as tightly as some of the others that I've used. And I think, actually, that can be a benefit, can't it?
Di: Well, yeah, it lays very well when you stitch, particularly when you’re stitching on any sort of linen, it lies beautifully. And that’s why you get the gradation so well, because of the softer texture of the wool. When you say softer, it’s still incredibly hard wearing, because we’re at the top end of the hard wearing wool in that, as Debs was saying, when we choose the wool to buy, it has to be at the very hard wearing end of the spectrum, because, of course, it’s going to last for a long, long time.
Di: Particularly if you put it in a carpet.
Gail: Yes, I'm sure. I suppose even things like church kneelers, that sort of thing, they're going to take wear and you'd expect them to last quite a while, wouldn't you?
Di: Hundreds of years. And I’m interesting that you brought that up, because that is one of the areas that very sadly has really died over the years since we’ve owned the business. Used to be a huge part of the business, too. There were embroidery groups in every church all around the country and huge ones in their cathedrals. But I’m afraid to say, with fewer people going to church, that is very much a very small part of our business now.
Gail: Yeah, that's a shame.
Di: Wonderful tradition.
Gail: I think it was something that used to bring the congregation together, but I think from what I've heard from other people, they would purchase kit, something that was agreed on, and they would all meet up and make yes, it's a shame if that died.
Di: Yes, it has, really. The cathedrals still have embroidery groups because there’s more money involved and a tourist business to follow. So I’m happy to say we’re still supplying quite a lot of the cathedrals, but church groups really have almost disappeared. Very sad.
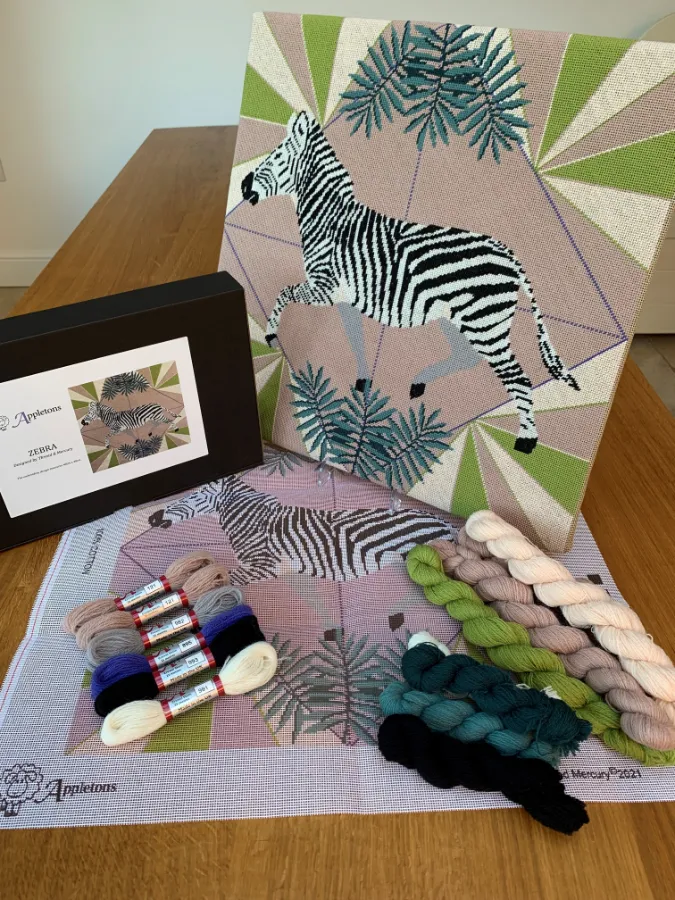
Gail: It is. And it's truly interesting that you bring up the way that things have come and gone, because you must have seen a lot of alteration and usage over, obviously over the time that the business has been around, but equally, just over the time that you have owned it.
Di: Probably these ten years have been the biggest change of all. We do get a lot of which is very exciting. We get wonderful public projects, which very much particularly in Scotland, where the great tapestry of Scotland was done, and the Preston Pans. I mean, huge projects these were, with 100 and 2160 panels in and around the country and around the world, we supply wool for large projects, which is wonderful to see, but I don’t know trends. Well, we can talk about that, too. What’s happening next? Because we have got some changes coming.
Debbie: Going back to your question, though, I think COVID had quite a. Big impact, actually, on the way in which people use our wool. So we found that we, like many craft companies, did incredibly well during COVID It was a very busy time for us. People were obviously at home. They were stitching more. It was very mindful. It’s been shown to have huge mental health benefits. And so I think what we’ve found has happened is that COVID had a bit of a switch on the way in which we sell our wool.
So prior to COVID, we were selling a lot more crewel wool. And crewel wool tends to be used more for embroidery because it’s a finer wool. Obviously, it takes longer to create your project if you’re using crewel wool, but you can get far more detail. Now, tapestry wool, if you’re stitching a needlepoint or a tapestry, it’s much quicker to use tapestry wool because it’s a thicker wool, obviously, and you tend to use larger holes per inch. And so what we found was that during COVID almost, we started selling more tapestry wool and crewel wool because we found that the age and certainly the ability of our customers was decreasing, which was amazing.
We were basically being people were picking up a needle and thread who hadn’t previously so we were tapping into a whole group of people who hadn’t previously thought about doing tapestry, which was absolutely fantastic. And often it was going into a younger age group, a little bit like knitting went completely bonkers, didn’t it, during COVID And we found the same with tapestry. And so, because of that as well, because we’ve tapped into a much younger market and also the very much the sort of mindful stitching, the fact people are finding it incredibly therapeutic. We’ve noticed that our colours have evolved as well, so we’re selling a lot more bright, funky colours than we were perhaps ten years ago. Our colours mean we still sell all of our colours, but we’re finding that some really vibrant colours, some really contemporary designs are now taking off. So I’d say that’s been quite a change. Would you agree, Diane?
Di: Absolutely, yes, which is a wonderful thing. I mean, I couldn’t be happier about that, because to see where we’re going, I don’t know if you’ve looked at our kits and you’ve got pictures, but our range of authors kits, which are pretty spectacular, have been hugely successful. And that’s definitely appealing to a younger audience. Yes, I can well imagine the colours.
Gail: I can well imagine. COVID was a really well, obviously a very worrying time in some ways, at a very interesting time for crafts, wasn't it? There was a lot of change. I think, as you say, people suddenly had more time on their hands.
Di: I think what’s more exciting, though, is the fact that obviously when we know from our figures is that an awful lot of people who did take it up in COVID didn’t then stop when COVID finished, but have carried on that’s hugely exciting for us. People are getting the bug, which I’m loving seeing.
Gail: Yes, I think I could agree with that in our business as well. Obviously, with the online learning that we had a very busy, very busy coach period and it's taken a little bit of adjustment since. But it is lovely to see more people and, as you say, younger, from a younger age group, enjoying and also, I think, managing to benefit from some of the side effects of crafts, because it's very soothing, it's very mindful in what is quite a stressful age. I think it's a lovely way of just taking some time out for yourself and being able to put your mind to rest for a little while.
Debbie: Yeah, absolutely.
Di: Without a doubt. Yeah, absolutely.
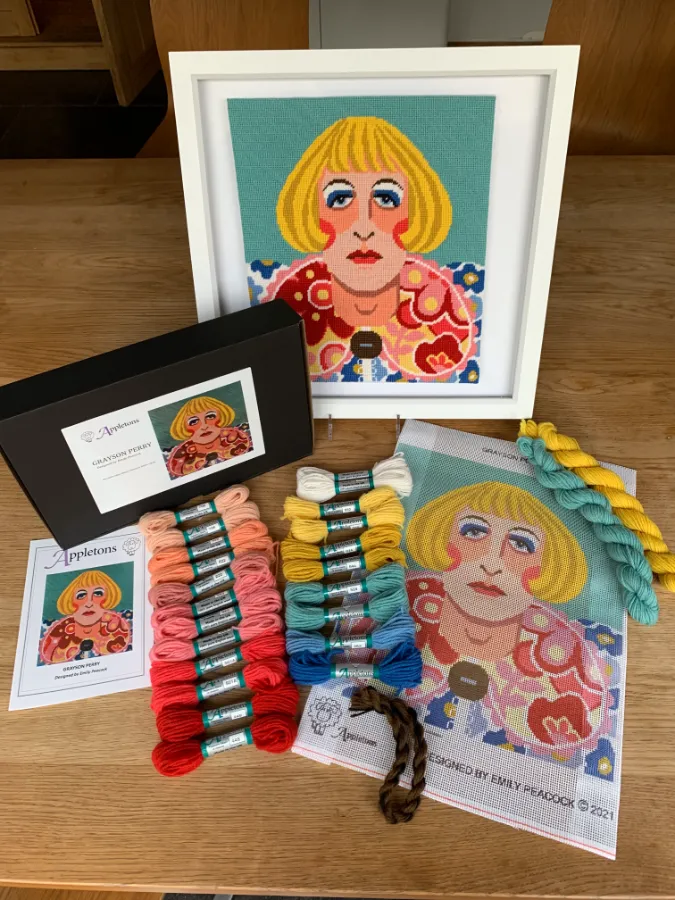
Gail: I would have thought, especially with tapestry, because it is quite a repetitive, because you're using one stitch all the time, so it is a very mindful thing to do.
Debbie: Yeah, absolutely. I say it’s very mindful. I don’t think Di is finding it very mindful this week. Oh, dear.
Gail: Why not?
Di: I’m speed stitching at the moment.
Debbie: We’re launching some new designs, which is so exciting, but I’m nagging everybody because I’m trying to do the photographs for the labels for the kits, which means I need all of these stitched. So everyone’s under huge amounts of pressure to stitch very quickly.
Di: Be mindful about that.
Gail: So can you tell us a little bit about what will be on the new designs?
Debbie: Yes, absolutely. We’re so excited. So, in the past, when you buy a tapestry, obviously you buy it, you get your wool, you get your canvas and then you do your tapestry and you have to decide, are you going to turn it into a cushion? Are you going to hang it on the wall? You’re going to put it in the back of your cupboard? And think about it. Metre, which is what a lot of people often do. And so we thought, right, we need to give people an entire experience so that at the end of their stitching, they have a product which they can immediately put on display.
So we’ve designed a range of boxes. So we’ve got a memory box, which is sort of little bit bigger than a four size. We’ve got a sort of a large trinket box and we’ve got a small trinket box. And the boxes are being handmade in the UK because we are so desperate to make sure that everything we do stays in the UK.
So they’re being handmade in the UK. And we’ve created a range of for our small trinket boxes, we’ve had a botanical artist has designed some absolutely beautiful flowers, which can be stitched quite quickly because they are using crewel wool, two strands of crewel wool, but they’re quite small. And so how many hours would you say it would take to stitch? Di would be a lot quicker. Oh, I couldn’t possibly say it’s not a huge component.
Di: No.
Debbie: And so you could do it if you would really focus probably in a week or so.
Di: Yeah, definitely.
Debbie: So we’ve got these stunning, stunning designs, which then once you stitch them, you can just pop them in the lid of your box. So the lid of the box is a little bit like a frame, so you can pop it in the lid of your box and hey, Presto, your craft is on display. And you’ve got a really nice practical.
Di: Or you can do it as a present.
Debbie: Yeah. So we’ve got a range of so we’ve got these four beautiful botanical flowers on the small ones and the larger trinket boxes, we’ve gone geometric. So we’ve got a range of stripes and hearts. And they are beautiful, really lovely. And then for the big one, we’re doing these beautiful sort of circles. But again, it’s a memory box and you can customize that and put an initial in the middle. So we were thinking it would be quite good for a new baby box or for somebody as a gift, and their initial in it.
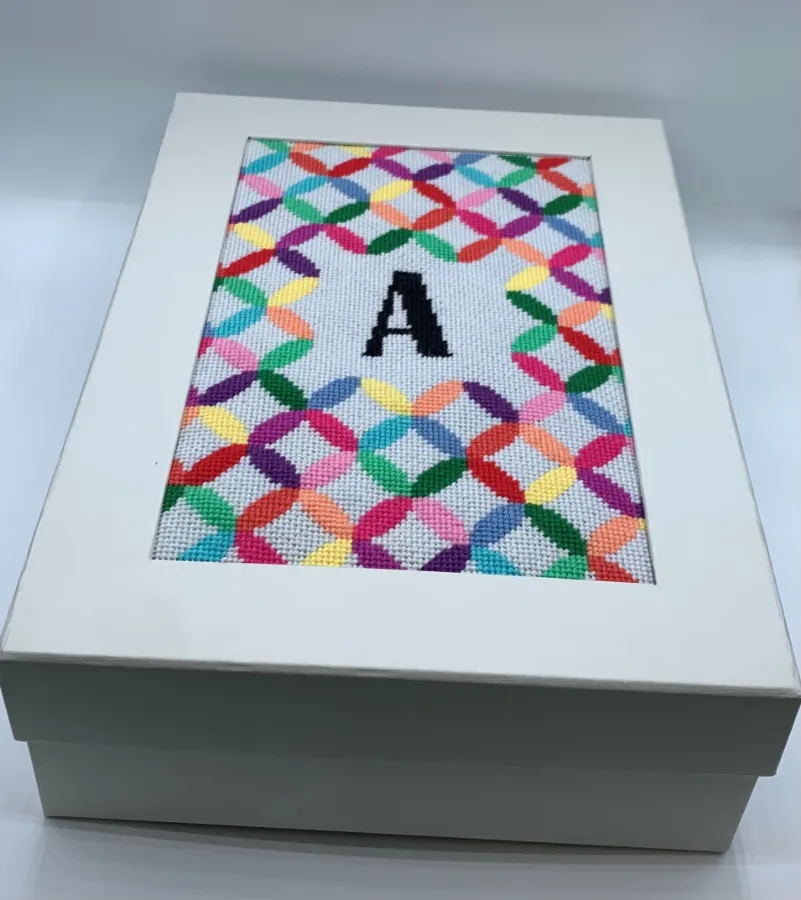
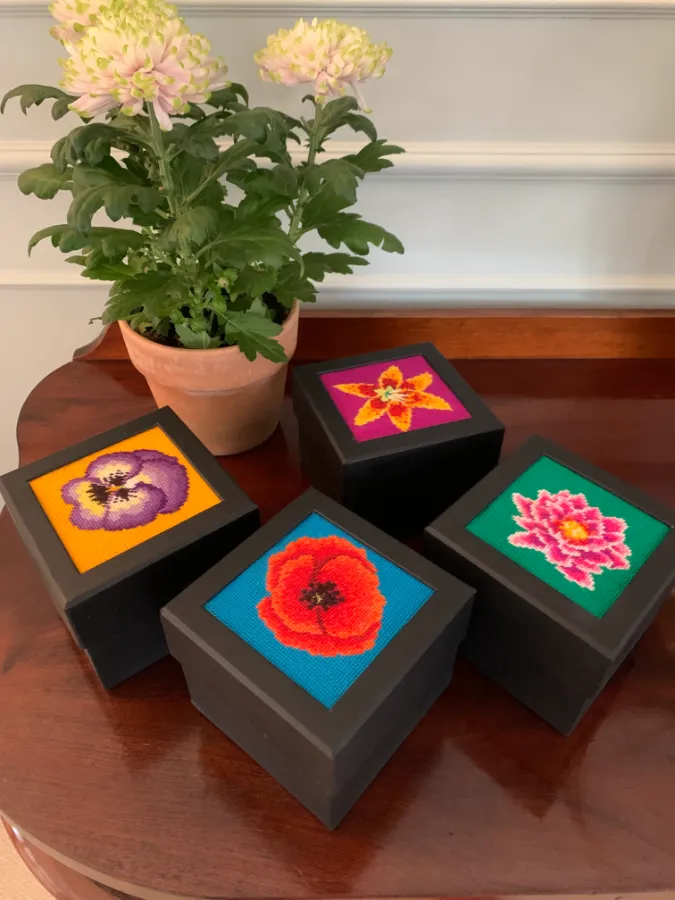
Gail: That sounds lovely.
Debbie: So they’re really lovely. Little bit under pressure this week to get next week. I can imagine.
Gail: It's not easy, speed stitching, is it?
Di: Satisfying.
Gail: It's quite a lot of work just getting to a show, isn't it? And with everything you need with all of your samples.
Debbie: Yes, it is. I’m right in the thick of it at the moment. Has anyone ordered the electrics? There’s so many things have we got the have we got the van hired? Yes, we’ve got the van hired, the parking place. So yes. Have we designed the stand? Yes, there’s quite a lot of work.
Gail: Yes, I can well imagine. And are you both going?
Debbie: Yes, the whole team’s going. So we’ve got a rotor drawn up to make sure that everybody’s got their taking their turn. Is that Alexandra Palace? Which is a bit of a difficult one to get to, isn’t it’s? Not straightforward, but yes, we’ve got our.
Di: Parking spaces and we’re sharing our stand with one of our designers, our main designer, Emily Peacock, who we’ve shared a stand with before at the Stitch Festival. So she will be there every day and she will be stitching on the stand, too.
Debbie: And she has some amazing designs and.
Di: It’S fun to be there with Emily.
Debbie: And she’s a laugh.
Gail: I know that you mentioned right at the beginning of our chat that the company used to dye wool for William Morris. Do you ever do any kits or projects that are William Morris based?
Di: Well, you know that one of our designers is Russell, one of our main customers, and really, she has cornered the market because her William Morris are the best. So we certainly wouldn’t try and repeat those. So there you can get the strawberry thief and all the very famous William Morris design. So she’s using the same colours
Debbie: Absolutely.
Di: The same colours that were there in 1856.
Debbie: She predominantly uses crewel wool, but then we have another designer or another company Bothy Threads, and they also do a range of William Morris that using tapestry wool, which is very accessible as well. So, yeah, we don’t feel like we should do that because it’s sort of already being done, using it by some of our fantastic customers.
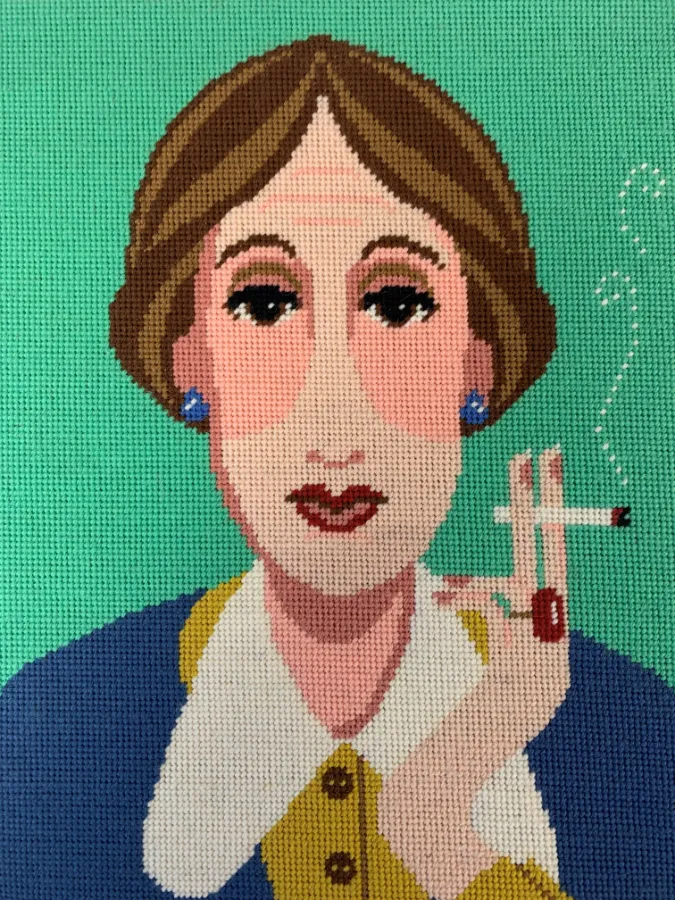
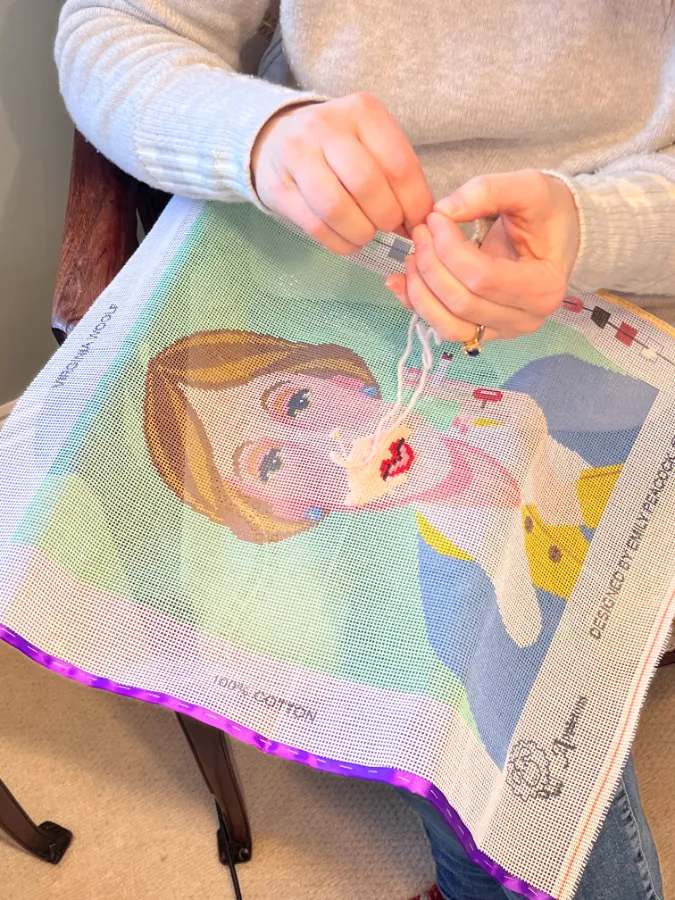
Gail: So really, when you're looking for commissioning anything new, you've also got that extra thought in the back of your mind that you don't want to step on any customers.
Di: Absolutely.
Gail: That must be a challenge.
Debbie: Well, not really.
Di: I mean, I think designers can go on finding new and exciting projects, and that’s what we’re trying to do, too.
Debbie: You’re right, though, because we have now just recently launched a retail arm, so we’re selling retail as well to our customers. And we were very conscious that we didn’t want to step on any of our customers toes. We are always aware that we’re working alongside and with our wholesale customers and we don’t want to be working against them. So, yeah, it’s a team effort.
Gail: Yeah, I can well imagine. So, obviously you've got the show coming up next week, but do you have any other plans for the future?
Debbie: It’s a very busy time at the moment. Can’t look beyond next week slightly? I can’t look beyond next week. But we are also looking to as I’d mentioned earlier, we’re looking to put everything on cone. So we have had a lot of our customers, particularly the Weavers, were very keen to get wool on cone. So we’ve had to change the way in which, as I said, we’re still hank dyeing. Absolutely. But instead of dyeing in our small hanks, we’re dyeing in much larger hanks.
And then we are then turning them into small hanks after they’ve been dyed, which means that all of our wool can be sold in small hanks. So sort of retail hanks on cone, in sort of half kilo cones or in skeins. Now, the reason that’s important is if we maintain dyeing in the smaller hanks, you can’t then rejoin the wool back together again and put it into sort of bigger hanks to put onto a cone. So that’s a change in the way we’re working.
We are constantly looking at new colours. Should we put new ranges out there? I think the next range that we’ll be doing will be a new range of grays, although that is sort of on my list of things to do after the show. So we’re always looking at new colours. We’re always looking at we’re launching, as I said at the moment, ten new designs. And that’s quite a lot for us to do in one go. But we will be continually looking at launching new tapestries. Yeah.
Gail: When you actually launch new colours, do you just allow them to increase the size of your range or do you withdraw some as well.
Debbie: Okay, that’s a really interesting question because yes, so obviously we can’t just keep going, increasing, increasing, increasing, because we just would run out of warehouse space. But we’re again very mindful of the fact that we don’t want to upset people and we don’t want to discontinue a colour that perhaps they’re using in a kit or perhaps we don’t want to upset we don’t want a customer to come to us and say, as I said, I’ve got this tapestry that my great auntie did, and I want to redo it. Do you still do one, four, eight? We want to be able to say, yes, of course we do.
So what we do is we will only discontinue a colour if and it has to meet both this criteria, if we sell very little of it and when we dye wool, we have minimum quantities to dye because you have to fill a VAT. So really, when we dye wool, the minimum we would ever dye would be 15 kilos of it. So if we are selling less than a kilo a year, you can see how it makes it quite unsustainable to keep it. But we would keep it if we don’t have an almost identical colour. So we will only discontinue wool if we’re selling a really tiny amount of it, and we have an almost identical colour in the range. And that can sometimes happen.
So we can sometimes find that we’ve got colours that are almost identical that are in different ranges. And so in that case, we would then discontinue it, but we don’t really like doing it. We’ve only ever once gone through a sort of discontinuing process. And yeah, we had a few people that had a problem with it, but actually we were able to overcome them. So in answer to your question, no, we don’t just keep adding and adding and adding and adding and never discontinuing because otherwise we would need an insanely large warehouse. But we would only discontinue if we felt that it wasn’t going to have an impact on our customers.
Gail: Yeah, I know. I've spoken to many people over the years that they get partway through a tapestry. They perhaps haven't necessarily always used the correct stitch to do it with. I'm sure that you recognize that one.
Debbie: We get the same, I can imagine.
Gail: So instead of using, obviously, half cross stitch, they're using tent stitch or whatever, and they run out part way and they need to buy some. It's a different dye lot. Do you have any tips for them about how they could integrate one with the other?
Debbie: Well, I’m going to answer that from a practical perspective then, with the tips. I don’t know if Di might have a tip or she has. So what I would say is, firstly, I check the wool in and I’m really annoying about how close it has to be to what I say is the standard. So I have in the office a huge amount of boxes that have got all of our standards in, and that is like, everything has to match the standard. So, first of all, I’m pretty confident that if you order another colour, it shouldn’t be discernible the difference. If you absolutely want to be careful, you could always send us a snippet of the wool that you are trying to match, and we would go and have a look at all of the wool that we have in that colour. And it might be that we have two or three dye lots on the go at the same time, depending on how much we sell of a particular colour. So we would try and match it as closely as we could. Now, I’ll pass over to Di for.
Di: Maybe a more practical well, obviously, the problem occurs mostly when people say, oh, I found this tapestry at the back of my granny’s cupboard.
Gail: Yes.
Di: And now she’s died, and I really want to finish it. And it’s from 1953. Well, there is no way that the dye lots are going to be the same. Obviously, my only tip it’s very hard to help if it’s tapestry wool, because you’re going to be stitching up close. My only tip with crewel wool is that if there is some there, you can split the strands and use the new one. So have one strand of the old and one strand of the new and then gently merge it away from the way you were stitching. And that can work. I mean, we’re talking background now. If you’re doing an old fashioned tapestry, that’s about the best that we can do. Other than that, you’re in for a lot of unpicking, I’m afraid.
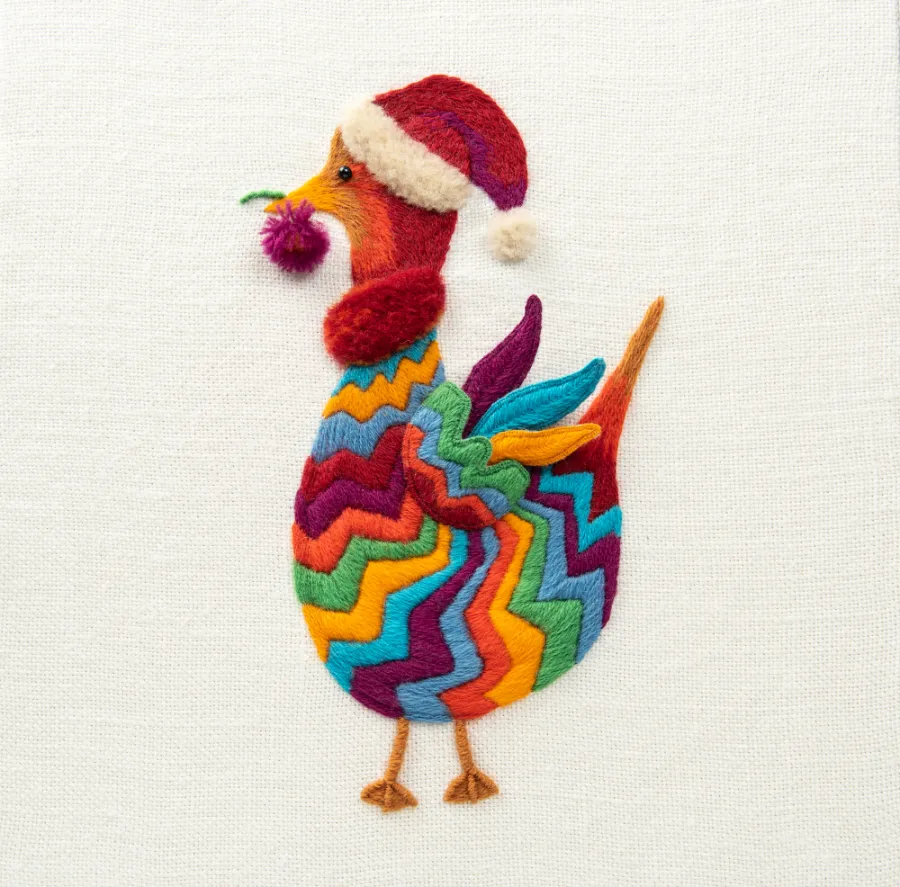
Gail: Yes. I suppose the advice that I've given to people in the past is to try and do an alternate row old new, if you have enough.
Di: Exactly. But with crewel, you can split it and then you can have one one, and that works quite well. And you get a sort of nice textured, sort of tweedy finish, and it’s rather nice. Anyway. It is a problem that comes up quite a lot.
Gail: I'm sure it does. So as far as I know, we're sort of probably coming to the end. I'm sure you're probably quite glad about that, because if you've got people waiting.
Debbie: To come into the office.
Di: They’ve been banished, they’re busy picking orders.
Gail: Well, hopefully they're doing some speed stitching for you for next week. But I just wondered if you had any sort of anecdotes or a short story to finish off with.
Debbie: Oh, my God.
Di: Probably most are unprintable.
Debbie: When you first bought the company and you were packing and fell in the.
Di: Box oh, I did. And also when we bought the company and we moved the wool up here and we found a packet of cheese.
Debbie: And onion in one of the bags.
Di: The wool was in a pretty bad state when we moved. It was quite a challenge, I have to tell you. I’m sure, all change now, but there.
Debbie: Was quite a funny can I tell.
Di: The story about your box
Debbie: So this is probably nine years ago. No, it’s been ten years ago. So the company moved sort of Blockstock and barrel, obviously, from London, near Oxford, and over that time we’d gone. I think he’d stopped fulfilling orders, hadn’t he? And so he’d stopped fulfilling so we had this mountain of orders to fulfill and obviously we had to get it up and running, we had to put the wool know, we had to know exactly. And we were out of stock of so many colours at the time, because when we picked the wool up, we are now almost never out of stock of anything. But then we had thousands well, not thousands, obviously, but loads and loads of colours that we had to get dyed very quickly. So consequently, we had all these orders piling up. We were trying to keep the customers happy, trying to get them out as quickly as possible. So I think, Di, you were working weekends, weren’t you?
Di: Absolutely. 24/7.
Debbie: Yeah. And we had these huge boxes that we would fill with skeins and we had a lot of orders for America. So Di was filling this box with skeins, and as she leant over the box, because it was so deep, she actually completely fell this isn’t actually, when I think about it, she completely fell in the box, but couldn’t get herself out of the box.
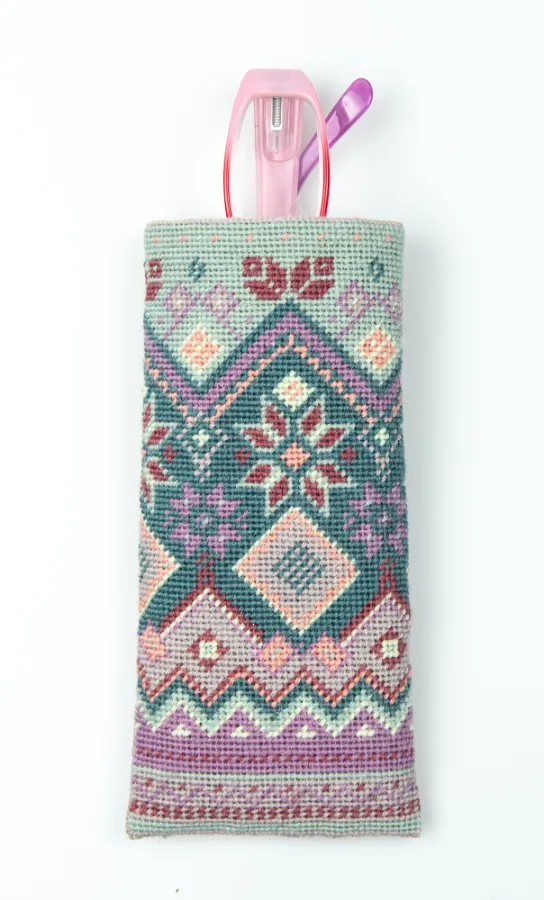
Gail: Oh, my goodness.
Debbie: Poor Di had broken a no, she was stuck with her legs, like, laying in the air in this box. Fortunately, she wasn’t on her own. So did you have Pete and pull me out? Pete and Colin had to pull her out, but they couldn’t pull her out without laughing.
Di: Well, they were laughing so much they didn’t know what to do. Anyway, they got me out and I thought, God, that hurts. And I found I’d broken two ribs, actually.
Gail: Oh, my goodness. The things that we do.
Debbie: Customers dedication to getting the order.
Gail: Dedication, absolutely.
Di: Those days are over, thank God.
Gail: You must have wondered, I suppose, in that process, what on earth you’d done? Why did I buy this business?
Di: Believe me, I did. Sleepless nights thinking, what have we done? And how long it would take to turn around? But the best thing that happened was that we employed some wonderful people, one of which sitting next to me, Debbie and Caroline, who from day one. And it seems that anybody who ever joins Appletons never.
Gail: It must be a nice place to.
Di: So there we are.
Gail: Well, thank you so much for joining me. It’s been a complete pleasure talking to you and especially now that I know what you’ve the pressure that you’re under for next week.
Debbie: Lovely to talk to you. Bye. Close.